CMMS Information
CMMS Information
Contact Information:
MaintSmart Software, Inc.
Phone: Toll-Free in the U.S./Canada +1.888.398.0450 . Outside the U.S.A. +1.541.751.0450
Address: 66164 Homestead Rd., North Bend, OR 97459, USA
Email: sales@cmms.org
International Contact: Skype ID: “maintsmart”
Purpose of MaintSmart CMMS: Manage and maximize the efficiency of any maintenance operation in any plant (or other entity) or multiple plants (or entities) and prolong equipment life. MaintSmart was developed by a maintenance manager with over 25 years combined experience in equipment maintenance and software engineering. See our capability statement.
CMMS Information and Technical Description: MaintSmart is available as cloud-based, desk-top stand-alone, LAN, WAN, with a web-based work request module. MaintSmart is a database front-end containing over 150 tables and over 2000 stored procedures. MaintSmart uses either Microsoft Access or SQL Server (2005-2016) as it’s database. If the Access option is selected the database drivers and file are free and Access is not required to fully use MaintSmart. This software is a stand-alone Windows application and does not require any other programs (such as Access to function). System Requirements
Competition Product Comparison: MaintSmart CMMS is fully self-contained. NO extra modules or applications to purchase! This CMMS software is simple to use and benefit from. The CMMS archives, analyzes and reports on: work orders, downtime (equipment failure), reliability analysis, preventative maintenance (PMs), inventory management and usage, purchase orders and receiving, equipment and personnel skills. Review several CMMS testimonials from our users then try it for yourself. We are certain that you will find our solution to be superior in every way, including price.
Toll-Free Phone and Email Support: MaintSmart comes with toll-free phone and email support for the first 60 – 365 days. Support is completely free during the evaluation period.
CMMS Training
Training is available but not required. Approximately 35% of our users elect to be formally trained. Training may be by Go-To-Meeting, onsite, offsite, formal, structured, informal, question/answer or one on one consulting.
Basic Features: A powerful tool for equipment management and preventive maintenance. Uses reliability analysis to suggest PM tasks and intervals . Tracks, analyzes and reports on: break downs, preventative maintenance (PMs), work orders, inventory, purchasing, equipment, production schedules, production wages (very quick entry, used by reliability analysis) and other CMMS information. This data provides the real cost of owning any given piece of equipment. By knowing what equipment costs to own during any given time period the user is able to determine appropriate steps to take to reduce this cost and increase efficiencies. Changes can then be tracked to determine if further changes are needed.
Flexible: Can be configured by the user to work in any manufacturing or equipment maintenance environment. Allows for up to 900 separate plants (or other entities) with up to one million separate pieces of equipment in each plant. This enables the CMMS information data bank for each Plant to be kept separate from the CMMS information of the others. Unlimited employees may be linked to unlimited skills each. Skills are user defined as are tasks, equipment, departments, inventory, break down causes and fiscal periods. MaintSmart’s equipment hierarchy may be defined by the user. Click here for examples.
Fast: Data entry is simple and fast. Shortcuts for repetitive tasks. Drag and drop task and equipment lists . Logical grouping of some data items allows groups of data to be applied with one action. Drop down boxes offer available possibilities only and provide record validation.
Secure: Administrator may create any number of different user groups allowing access to users as needed. Access controls may be applied to viewing, querying, adding records, editing or deleting records, and printing. This allows all employees of the maintenance department some level of access to the CMMS. Access to program is logged.
CMMS Information Reporting
CMMS Reporting: Crystal Reports 2010 is used for reporting purposes. Over 250 separate reports are available in addition many of these reports accept user defined data parameters. All data directly exports to Excel or a web page. The CMMS is an automation controller for MS Excel. Though Excel is not required it does enhance MaintSmart. Data may be automatically loaded into Excel to take advantage of Excels analysis and charting capabilities. This CMMS also provide Overall Equipment Effectiveness or OEE, OLAP, Online Analytical Processing, SQL queries, data grid filters and more.
Powerful and Flexible Data Analysis: Overall Equipment Effectiveness (OEE), Online Analytical Processing (OLAP), data cubes, parameter queries and ad hoc queries are available throughout the program allowing the user to analyze break downs, work orders, PMs, inventory, production schedule history, technician wage history and more. Reports are available for nearly all queries. Reports include graphs where appropriate. Queried data may also be imported into MS Excel with the click of a mouse. Inventory audits and reordering is simple and accurate.
Reliability Analysis: This feature enables the plant engineer to make job assignments based on proven machine failure data. AMMSA failure analysis methods are used to optimize PM schedules and track progress. This takes to guess work out of PM scheduling and provides for fewer breakdowns and more efficient labor allocation. OEE also included with base module.
Guaranteed: We are so confident that MaintSmart will exceed your expectations that we offer a 15 day ‘no questions asked’ warranty. The MaintSmart Trial program may also be downloaded and tested for 30 days. This is the full program unlicensed and comes with sample databases.
MaintSmart Corporate Offices are conveniently located within 1/10 mile of the airport.
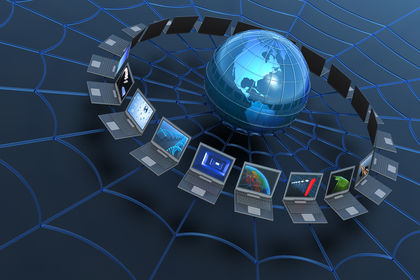